Ciśnienie | Ciśnienie tłoczenia 1 do 3,5 bara |
---|---|
Moc silnika: | 30 do 500 kW |
Poziom hałasu | 70 do 79 dB (A) |
Technologia | Sprężarki śrubowe z chłodzeniem wodnym lub powietrznym ZE/ZA 3-6 i ZE4VSD |
Wydajność | 128 do 2058 l/s, 272 do 4360 stóp3/min |
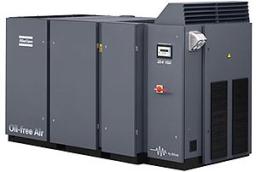
Sprężonepowietrze o niskim ciśnieniu jest często podstawowym elementem procesuprodukcyjnego: transport materiałów sproszkowanych i masowych,separacja pneumatyczna, uzdatnianie wody, mieszanie materiałów,napowietrzanie, chłodzenie i osuszanie… Ogólna niezawodność procesuprodukcyjnego to jedna z podstawowych kwestii.
Znaczącepolepszenie procesu osiągnięto przez wykorzystanie niskociśnieniowychsprężarek : zakres ZE (chłodzone powietrzem)/ZA (chłodzone wodą).
- Element śrubowy bezolejowy
- Powlekane wirniki
- Kompleksowe wyposażone
- Tłumik powietrza na wylocie
- Wbudowany rozrusznik
- Osłona wyciszająca (wersja standardowa)
- Fabrycznie zmontowana tablica rozdzielcza
- Zawór zwrotny
- Silnik zabezpieczony przed dostępem wody i kurzu klasy IP 55
- Wylot pochłaniający drgania
Korzyści
- Całkowicie bezolejowe powietrze
- Gwarancja ciągłej wydajności
- Gotowość do pracy bez ponoszenia dodatkowych kosztów
- Bez konieczności zakupu kosztownego wyposażenia dodatkowego
Prosta instalacja
Łatwa i tania instalacja dzięki konstrukcji niewymagającej stosowania fundamentów ani śrub.
Kompaktowy zespół, który wystarczy jedynie umieścić w wybranym miejscu i podłączyć (wszystkie przyłącza dostarczane są w standardzie).
Sprężarki ZE-ZA zostały również opracowane pod kątem łatwości integracji dodatkowych elementów zgodnie z wymogami poszczególnych zastosowań. Więcej informacji można znaleźć na stronie poświęconej opcją niestadardowym
Sterowanie i monitorowanie
System sterowania i regulacji Elektronikon®.
Inteligentna technologia gwarantująca niezawodność i bezpieczeństwo pracy
-
Czujniki elektroniczne zamontowane w najważniejszych miejscach sprężarki przekazują dane o temperaturze i ciśnieniu do sterownika mikroprocesorowego. Mikroprocesor monitoruje stan całego układu sprężarki na podstawie wskazań czujników oraz automatycznie reguluje i steruje sprężarką w celu uzyskania optymalnych parametrów i sprawności.
-
System Elektronikon® wyposażony jest w funkcję „kontrolowanego zatrzymania” wyłączając silnik sprężarki po osiągnięciu ciśnienia odciążenia lub wtedy, gdy przewidywany jest dłuższy okres pracy bez obciążenia. Oznacza to mniejszy pobór energii, niższe zużycie eksploatacyjne, dłuższe odstępy między konserwacjami i krótsze okresy nieplanowego przestoju.
-
Polecenia są przekazywane do sprężarki przez sensorowe przełączniki membranowe.
-
System Elektronikon® jest całkowicie zaprogramowany w fabryce i łatwo może być przeprogramowany, jeśli warunki na miejscu eksploatacji wymagają zmiany parametrów sterowania.
-
W systemie Elektronikon® można wybrać język użytkownika i język dodatkowy.
-
System przekazuje również z wyprzedzeniem wskazówki odnośnie wymagań serwisowych i pomaga z góry zaplanować przeglądy serwisowe.
Zasada sprężania
-
Zasada sprężania jest prosta. Dwa wirniki , jeden z czterema płatami, a drugi z sześcioma wyżłobieniami, obracają się wzajemnie się zazębiając. Pierwsza śruba obraca się o 50% szybciej niż druga. Zassane powietrze jest sprężane między wirnikami i obudową.
-
Współpracujące wirniki nigdy się nie dotykają dzięki precyzyjnemu mechanizmowi rozrządu, który utrzymuje minimalne luzy między powierzchniami wirników. Wyeliminowano w ten sposób efekt zużycia eksploatacyjnego, nie ma również potrzeby smarowania przestrzeni sprężającej.
-
Specjalne uszczelnienia zapobiegają ucieczce powietrza wzdłuż wału wirnika, a oddzielne uszczelnienia zatrzymują wyciekanie oleju z łożysk wirnika do komory tłoczenia. W rezultacie otrzymywane jest powietrze odolejone w 100% i bez pulsacji.
Akcesoria
Układy opcjonalne:
W przypadku niektórych zastosowań mogą być potrzebne lub korzystne dodatkowe opcje oraz bardziej wyrafinowane układy sterowania i obróbki powietrza. Dodatkowe akcesoria dla sprężarek ZE-ZA ułatwiają budowę bardziej zaawansowanych systemów i pozwalają ograniczyć koszty.
Jeśli potrzebne jest suche powietrze, Atlas Copco oferuje szeroką gamę osuszaczy powietrza.
W instalacjach wykorzystujących wiele sprężarek warto zainstalować automatyczny system sterowania i monitorowania typu ES.
Wiele instalacji opartych na sprężonym powietrzu o niskim ciśnieniu wykorzystuje suche powietrze wysokiej jakości jako jeden z czynników ograniczających ryzyko zanieczyszczenia produktu i uszkodzenia układu obiegu sprężonego powietrza.
Poczucie pewności dzięki automatycznym systemom:
Centralne systemy sterowania typu ES lub zdalne systemy monitorowania mogą służyć do jednoczesnego zarządzania wieloma sprężarkami o takiej samej lub różnej wydajności. Obliczają one z wyprzedzeniem zapotrzebowanie na powietrze i na tej podstawie przygotowują i uruchamiają instalacje sprężarkowe z uwzględnieniem maksymalnej efektywności, rozdzielając obciążenie i utrzymując niski zakres ciśnienia w celu zapewnienia najniższych kosztów bieżących.
System wyświetla informacje o stanie każdego zespołu i całego systemu, ostrzegając o problemach przed ich wystąpieniem i proponując określone działania serwisowe.
Wstępnie zaprojektowane układy, umożliwiające pełną integrację
Warianty dla zastosowań dostosowanych do indywidualnych wymagań:
Dzięki sprężarkom ZE-ZA w niepamięć odchodzi kosztowne, czasochłonne przeprojektowywanie. Z łatwością można przewidzieć wymagania dla różnych zastosowań. Konstrukcja urządzeń umożliwia bezproblemowe dodawanie i usuwanie dodatkowych elementów.
Odmiany sprężarek ZE-ZA bez wyciszenia są dostępne jako wariant alternatywny instalacji niewymagających kontroli hałasu.
Opracowane pod kątem ekonomicznego dostosowywania się do zapotrzebowania na powietrze
W procesach ze zmiennym zapotrzebowaniem na powietrze system regulacji w układzie pełne obciążenie/brak obciążenie steruje wytwarzaniem sprężonego powietrza w taki sposób, aby dostosować je do aktualnego zapotrzebowania i zapewnić pracę sprężarki przy optymalnej efektywności i jak najniższych kosztach. Regulator ustawia albo maksymalną wydajność 100% (całkowite otwarcie), albo 0% wydajności, co pozwala zmniejszyć zużycie energii w porównaniu z konwencjonalnymi systemami wydmuchowymi.
Zespół opracowany w sposób umożliwiający łatwe dodanie chłodnicy końcowej: :
Dla procesów wymagających zimnego powietrza:
Sprężarki ZE-ZA oferowane przez firmę Atlas Copco nie tylko pozwalają zaoszczędzić czas i pieniądze oraz uniknąć kłopotów związanych z wyborem i instalacją osobnej chłodnicy końcowej, ale również zawierają wszystkie niezbędne elementy wewnątrz obudowy, co eliminuje koszty montażu oraz pozwala zapobiec spadkom ciśnienia.
Zastosowania
Rola powietrza o niskim ciśnieniu w przemyśle spożywczym:
Należąca do koncernu Rhône-Poulenc fabryka Nutriciones Animales C.A., zlokalizowana w Burgos w północnej Hiszpanii, produkuje dodatki do pasz dla ryb, drobiu i bydła. Jeden z etapów produkcji wymaga użycia powietrza o niskim ciśnieniu. Proces ten polega na dodawaniu aminokwasów i właśnie w tym punkcie podstawowe znaczenie ma dostarczenie sprężonego powietrza. Od ilości azotu (obecnego w sprężonym powietrzu) dostarczonego do reaktora zależą wszystkie kolejne reakcje chemiczne oraz proporcje innych składników. Proces produkcji aminokwasów nie ma charakteru stałego, ale podlega ciągłym zmianom, szczególnie w fazie początkowej i końcowej. Tym niemniej absolutnie niezbędne jest dostarczanie sprężonego powietrza w sposób ciągły i przy stałym ciśnieniu 0,82 bara (sk.) (z tolerancją 0,005 bara). Sprężarką realizującą to zadanie w stopniu zapewniającym bezgraniczne zadowolenie klienta jest napędzana silnikiem bezstopniowym niskociśnieniowa sprężarka ZA5 firmy Atlas Copco. Ten niskonapięciowy silnik, sterowany przetwornikiem częstotliwości w zakresie od 24 do 58 Hz, napędza sprężarkę ze zmienną prędkością wynoszącą od 720 do 1740 obr/min. Podczas uruchamiania oraz przy minimalnej prędkości sprężarki sprężone powietrze jest kierowane do otoczenia.
ZASADA DZIAŁANIA
Dwa główne powody, dla których firma Rhône-Poulenc zdecydowała się na zastosowanie sprężarki ZA5 z napędem bezstopniowym, to:
- Bardzo wysoka stabilność ciśnienia przy różnych poziomach zapotrzebowania na sprężone powietrze
- Większa oszczędność energii w porównaniu z rozwiązaniami alternatywnymi, tzn. sprężarki odśrodkowej wydmuchującej w sposób ciągły nadwyżkę sprężonego powietrza
…i właśnie złożono zamówienia na kolejną sprężarkę ZA5 w takiej samej konfiguracji!
Bezolejowe powietrze o niskim ciśnieniu do produkcji bituminu.
Brak konieczności osuszania sprężonego powietrza.
Wdmuchiwanie odolejonego powietrza w bitumin:
ESSEN/MANNHEIM, październik 2001
Prawdziwy paradoks. Powietrze jest sprężane w sposób gwarantujący całkowite odolejenie w bezolejowych sprężarkach tylko po to, aby zostać wtłoczone w mieszaninę o dużej zawartości oleju. Ale tak właśnie dzieje się w zakładach firmy Goldschmidt w Mannheim. I nie bez powodu. Bitumin jest rafinowany przy użyciu tlenu. Dlatego też wtłaczanie powietrza zawierającego olej byłoby ryzykowne. Istnieje jednak jeszcze jeden powód stosowania sprężarek bezolejowych. Ale po kolei…
Goldschmidt TIB, koncern chemiczny z centralą w Mannheim, dokonuje rafinacji surowego bituminu pochodzącego z rafinerii ropy naftowej przy użyciu pozbawionego oleju powietrza o niskim ciśnieniu (1 bar), aby otrzymać bitumin o określonych właściwościach. Może on być dalej przetwarzany pod kątem nawierzchni drogowych, pokryć dachowych, uszczelnień fundamentów itp. Klasę bituminu określają dwie wielkości fizyczne — temperatura mięknienia i przenikanie (miara twardości). Celem rafinacji bituminu jest wytworzenie bituminu, który jest twardy nawet w wysokich temperaturach otoczenia, a jednocześnie nie kruszy się w niskich temperaturach.
Można to osiągnąć dzięki utlenianiu określonych składników bituminu w wysokich wąskich zbiornikach, zwanych przedmuchowymi instalacjami destylacyjnymi, w których odolejone powietrze jest przedmuchiwane od dołu przez ogrzany ciekły bitumin. Żądaną temperaturę mięknienia i przenikanie można ustawić przez określenie czasu trwania utleniania oraz wykorzystanie pewnych mieszanek olejowych.
Roczna produkcja utlenionego bituminu w zakładach firmy Goldschmidt wynosi ok. 40 000 ton. „W porównaniu z rafineriami dokonującymi rafinacji własnego bituminu, który powstaje zawsze jako najcięższa frakcja, może nie jest to duża ilość”, przyznaje specjalista ds. produkcji, „ale rafinerie dostarczają jedynie standardowe klasy bituminów, ponieważ produkcja odbywa się w sposób ciągły”. Dla odmiany, zakłady Mannheimers pracują w sposób przerywany, gdzie każda instalacja destylacyjna działa niezależnie. Umożliwia to produkowanie każdorazowo różnych klas bituminów i zaklasyfikowanie zakładu jako producenta specjalistycznego. „Nasze najmocniejsze strony to elastyczność i możliwość produkcji wszelkich możliwych klas bituminu”, mówi specjalista ds. produkcji Ernst-Michael Jaeckel”.
Aby móc realizować ten cel, zakład Mannheimers ma trzy przedmuchowe instalacje destylacyjne: dwie o pojemności 40 metrów sześciennych i jedną o pojemności 80 metrów, co odpowiada 35 i 70 tonom bituminu. W tych instalacjach destylacyjnych bitumin (w zakładzie i podczas transportu utrzymywany w temperaturze przynajmniej 180°C) jest podgrzewany do temperatury 230°C, tak aby mogło rozpocząć się utlenianie. Po rozpoczęciu reakcji egzotermicznej podgrzewanie można wyłączyć. Później bitumin musi być nawet chłodzony przez wtryskiwanie wody.
W czasie procesu rozdmuchiwania, który trwa od kilku godzin do jednego dnia, wtłaczane powietrze jest mieszane z masą bitumiczną, aż zostanie uzyskana mieszanina jednorodna. Długość okresu wdmuchiwania powietrza zależy od wymaganej klasy wytwarzanego bituminu. Dwie do trzech godzin przed zakończeniem pobierane są próbki pomagające określić dokładny moment, gdy proces należy przerwać.
Ale dlaczego powietrze wtłaczane w celu realizacji tego wybitnie olejowego procesu musi być pozbawione oleju? „Ze względów bezpieczeństwa”, wyjaśnia specjalista ds. produkcji. Przy sprężaniu bezolejowym nie ma potrzeby przygotowywania sprężonego powietrza. Może być ono używane dokładnie w takim stanie, w jakim opuszcza sprężarkę. „Schładzanie ciepłego powietrza tylko po to, aby następnie wtłoczyć je to gorącego bituminu, nie ma po prostu sensu”. Ale tak właśnie by było w przypadku zastosowania sprężarek ze smarowaniem olejowym. Regulacje prawne dotyczące zapobiegania wypadkom wymagają, aby wtłaczane do systemu sprężone powietrze zawierające olej rur miało maksymalną temperaturę 110°C. Przedmuchowe instalacje destylacyjne są całkowicie bezpieczne, ponieważ wykorzystanie pary wodnej eliminuje jakiekolwiek ryzyko eksplozji. Wydmuchiwane powietrze ma oczywiście wysoką zawartość oleju i silny zapach. Dlatego też jest poddawane spalaniu końcowemu, które z kolei zamienia ciepło na bitumin.
Pięć chłodzonych powietrzem, bezolejowych, niskociśnieniowych sprężarek śrubowych ZE 45 (każda o wydajności 238 l/s) dostarcza odolejone powietrze dla destylatorów pod ciśnieniem 2 barów. Powietrze z jednej sprężarki wystarcza dla każdej z mniejszych instalacji destylacyjnych, a większa instalacja jest zasilana z dwóch sprężarek jednocześnie. Piąta sprężarka służy jako urządzenie rezerwowe, ponieważ powietrze jest potrzebne w całym procesie przedmuchiwania. Zdaniem Jaeckela „Wykorzystujemy pełne możliwości sprężarek”. Nie ma automatycznego systemu sterowania ani komory ciśnieniowej. Sprężarki przypisane do poszczególnych instalacji destylacyjnych są po prostu włączane i wyłączane zgodnie z zapotrzebowaniem.
Zakład Mannheimers nabył pierwszą bezolejową sprężarkę trzy lata temu. „Dwa lata temu postanowiliśmy zastąpić starzejące się sprężarki śrubowe, chociaż w dalszym ciągu nadawały się do eksploatacji, czterema dodatkowymi sprężarkami ZE”, wyjaśnia Jaeckel. Mimo iż stare urządzenia również były bezolejowe, „po prostu były już przestarzałe”. Zastosowanie nowych urządzeń zwiększyło możliwości wytwarzania sprężonego powietrza o ok. 25%. „Pozwoliło to skrócić procesy nadmuchiwania i zwiększyć produkcję”, dodaje z entuzjazmem specjalista ds. produkcji.
Zakład dokonuje nie tylko rafinacji bituminu. „Klienci dostarczają nam surowiec, a my zamieniamy go w bitumin o dowolnych żądanych właściwościach”. Zakłady Goldschmidt TIB produkują głównie chemikalia nieorganiczne oraz powłoki antykorozyjne dla rur.
Przemysł cementowy
Dostarczanie sprężonego powietrza jest niezbędne w składowaniu i mieszaniu surowców w zakładach i kompleksie żwirowni firmy Blue Circle Cements (BCC) w Northfleet, w pobliżu Tamizy, w północnej części hrabstwa Kent w Anglii..
Dwudziestoletnie, hałaśliwe, przestarzałe sprężarki i zbędny system chłodzenia wodnego oparty na chłodnicy kominowej zostały zastąpione nowoczesną baterią ekonomicznych i energooszczędnych, przyjaznych dla środowiska, bezolejowych rotacyjnych sprężarek śrubowych. Dziesięć z tych zespołów zostało dostarczonych przez firmę Atlas Copco. Zainstalowano je w oryginalnym pomieszczeniu sprężarek, teraz całkowicie zmodernizowanym, w pobliżu miejsca, gdzie surowiec umieszczony w ogromnych zbiornikach szlamowych musi być utrzymywany w ciągłym ruchu.
Pięć z tych zbiorników mieści do 9500 mieszaniny kredy, gliny i wody. Trzy pozostałe mieszczą po 7500 ton mieszaniny gliny i wody. Sprężone powietrze w formie bąbelków jest przepuszczane przez mieszaninę, zapewniając równe mieszanie.
Sprężarki firmy Atlas Copco zostały wybrane przez dział techniczny po intensywnych analizach porównawczych dostępnych rozwiązań. Wybrane urządzenia to jednostopniowe sprężarki śrubowe ZA3, każda połączona z osobnym zbiornikiem szlamowym, mogące w ciągu minuty dostarczyć 16 m3 powietrza o ciśnieniu 3 barów.
Każda z tych przyjaznych dla użytkownika sprężarek pracuje autonomicznie i zawiera wbudowany system monitorowania i sterowania. Niezawodność konstrukcji oznacza możliwość pominięcia zespołu rezerwowego. Ponadto ciepło pochodzące z wewnętrznych chłodnic sprężarki jest przesyłane do sąsiedniego zespołu wymiennika ciepła, który kieruje 90 kW gorącego powietrza do pobliskiego budynku zasobników kredy, co pomaga zapobiegać zamarzaniu surowca w czasie zimy. Dostarczanie sprężonego powietrza ma znaczenie kluczowe, ponieważ brak powietrza oznacza brak produkcji cementu.
Oprócz sprężarek ZA3 w zakładzie firmy BCC w Northfleet zainstalowano sprężarki serii LE9N oraz osuszacze powietrza wykorzystujące środki osuszające, które dostarczają powietrze dla przyrządów oraz szeregu działek pneumatycznych służących do usuwania wszelkich blokad materiałów w systemie zasobników kredy.
Opisana instalacja stanowi poważną inwestycję w wydajność produkcji, która pomaga utrzymać wysokie standardy jakościowe wyrobów firmy Blue Circle Cement.
Komentując wiele korzyści operacyjnych, jakie dają wprowadzone rozwiązania, rzecznik firmy BCC stwierdził: „Nowy system wytwarzający sprężone powietrze jest nie tylko cichy, energooszczędny i łatwy w obsłudze, ale jest również prosty w konserwacji, co pozwoliło znacznie ograniczyć poziom zapasów części”.
Powietrze o niskim ciśnieniu i kopiarki:
Podczas wykonywania kserokopii nikt raczej nie myśli o tym, że w pewnym momencie odolejone powietrze pod niskim ciśnieniem może odgrywać znaczącą rolę w reprodukcji dokumentu. W rzeczywistości zaś jeden z etapów produkcji tonera, który jest stosowany w kopiarkach, stanowi typowe zastosowanie powietrza o niskim ciśnieniu. Oto raport z naszej wizyty w zakładach produkcji tonera firmy Rank Xerox w Madrycie, w Hiszpanii.
PRODUKCJA TONERA
Należący do firmy Rank Xerox madrycki zakład produkcji tonera jest jednym z wielu zakładów firmy wytwarzających toner na świecie. Zakłady te pełnią rolę ośrodków, w których produkowane są „tonery” (tworzone na bazie sadzy materiały powodujące pojawianie się czarnych liter na papierze). Jednym z etapów procesu produkcji tonera jest mielenie kompozytu tonerowego za pomocą sprężonego powietrza pod wysokim ciśnieniem, znane jako mikronizacja lub mielenie w strumieniu powietrza. Zdaniem Carlosa Rodrigueza, dyrektora ds. infrastruktury technicznej zakładów w firmie Rank Xerox, równie istotne jest sprężone powietrze o niskim ciśnieniu.
ZASTOSOWANIE POWIETRZA O NISKIM CIŚNIENIU
Wykorzystanie powietrza o niskim ciśnieniu w procesie produkcji tonera to niezwykle błyskotliwe rozwiązanie zapewniające ochronę łożysk kulkowych i rolkowych mieszacza zamontowanego w zbiorniku mieszania w reaktorze. Przy stałym ciśnieniu 2,5 bara (sk.) łożyska są uszczelniane przed dostępem mikroskopijnych cząsteczek tonera (20 mikronów). Carlos Rodriguez stwierdził: „To najbezpieczniejszy sposób uszczelnienia, ponieważ jest to rozwiązanie o nieograniczonej długości działania i niewymagające konserwacji”. Jak powszechnie wiadomo, mikroskopijne zanieczyszczenia dostające się do smarów szybko powodują zużycie i uszkodzenie łożysk. W omawianym zastosowaniu sprężone powietrze o niskim ciśnieniu jest zapewniane przez sprężarkę ZA5 firmy Atlas Copco, napędzaną silnikiem bezstopniowym. P. Rodriguez wybrał ten typ napędu głównie ze względu na oszczędność energii:
- Pewność uzyskania stałej wartości ciśnienia bez konieczności wydmuchiwania nadmiaru powietrza na zewnątrz (co ma miejsce w przypadku sprężarek odśrodkowych) oznacza brak strat energii.
- Oszczędność energii dzięki optymalnemu poborowi mocy przez silnik.
MOŻLIWOŚCI SPRZEDAŻY
W dalszym ciągu wiele zakładów produkcji tonera firmy Rank Xerox (jak również zakłady innych producentów) na całym świecie w systemie uszczelnienia stosuje sprężone powietrze o wysokim ciśnieniu. Dzięki korzyściom wynikającym z możliwości ograniczania zużycia energii przez zastosowanie niskociśnieniowych sprężarek napędzanych silnikiem bezstopniowym ta interesująca i ekonomiczna alternatywa stanowi obszar dodatkowych możliwości sprzedaży niskociśnieniowych sprężarek ZE/ZA firmy Atlas Copco.